April 2019
Stainless steel vs carbon steel
Is stainless steel better than carbon steel?
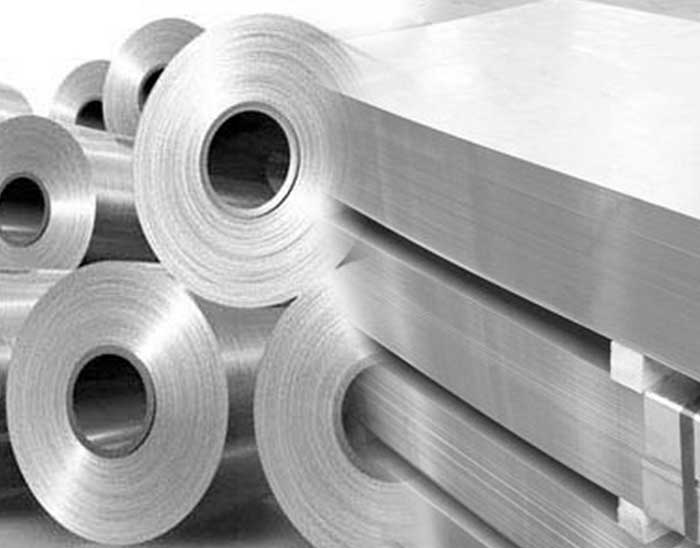
Is stainless steel better than carbon steel?
As a materials engineer the answer to this question is a classical two handed one. “On the one hand, yes. But on the other hand, no.”
This isn't indecision, but fact. There are applications where stainless steel will be more cost effective and give superior performance than carbon steel, but equally there are applications where carbon steel is more cost effective and gives better service than stainless steel. So how does this make sense?
To understand the scenarios where stainless steels are better than carbon steels, we must first understand what a stainless steel is, and this takes us back to 1912 Sheffield. Harry Brearley ‘discovered’ stainless steel while working in the Firth Vickers research laboratories there. He was experimenting with adding chromium to carbon steels to see what effect it would have. Legend has it one of his samples didn't etch, so he threw it on a scrap pile and went home. Next day, when all the other samples had rusted, this one remained clean and shiny. It was a 12% chromium alloy and was the first recorded instance of a stainless steel.
Strictly, ‘stainless steel’ means any iron-based alloy containing more than about 12% chromium, because at this level the chromium forms a protective chromium oxide layer on the surface of the metal and basically it is this protective layer which imparts corrosion resistance to these alloys. Nowadays, stainless steel is commonly used to mean austenitic stainless steel, such as the 300 series alloys; 304, 316, etc. These materials contain typically 18% chromium and 8% nickel, the rest being iron and a few other bits. The structure of these alloys is referred to as being austenitic, because the nickel prevents the formation of ferrite (as found in carbon steels) as the alloy cools.
So austenitic stainless steel contains chromium and nickel (plus a few other additions, depending on the specific alloy being considered) and as both of these main alloying additions are expensive, so is the resultant stainless steel. However, cost does not indicate effectiveness. Handling high strength brine (sodium chloride solution), carbon steel performs in a predictable and cost-effective way, but with limited life. Stainless steel does not. It tends to pit and/or suffer crevice corrosion and may suffer stress corrosion cracking, all of which are unpredictable yet potentially catastrophic. Which would you rather use: a life limited but predictable, cheap carbon steel, or an unpredictable, expensive stainless steel?
Why is this so? Stainless steels rely on the protection of the chromium oxide layer. If chromium oxide is so good, why don't we use chromium for building chemical plants? The answer is that chromium is not an easy material to deal with, being hard, brittle and generally unfriendly to welding. However, using it as an alloying addition removes these issues and makes a relatively friendly material which can be cut, shaped and joined by welding.
The overriding problem with stainless steels of whatever composition is their dependence on the chromium oxide layer. This is because chromium oxide is severely attacked by four chemical ions, namely: mercuric, cupric, ferric and chlorides. While the first two can quite readily be avoided, attack by chlorides is the Achilles heel of stainless steels. So why not avoid chlorides? Simply because chlorides can crop up is so many different places and solutions in a modern world: sea water contains about 3.5% sodium chloride, coastal rain and fog contains chlorides from the sea. Normal UK tap water contains about 30ppm chlorides, not much until you appreciate that as little as 2ppm can result in chloride stress corrosion cracking of austenitic stainless steels. Even fingerprints can lead to failures, because human sweat contains chlorides. And I haven't even mentioned ferric ions, not because they are very common, but because the result of attack by chlorides results in the formation of ferric chloride, effectively making a more corrosive corrosion product than the original corrodent. So, we are learning to live with the risk and consequence of failures and manage their propensity.
One way of doing this is by changing the alloy composition.18% chromium, 8% nickel in iron is susceptible to chloride stress corrosion cracking, but 22% chromium, 5% nickel in iron is far less susceptible and 25% chromium, 7% nickel in iron is almost immune. The problem with these latter two alloys is they are more difficult to cut, shaped and weld, making fabrications more expensive.
The other important and often overlooked aspect, even when in so called ‘non-corrosive’ environments, is that in order to maintain their protective oxide layer, it is necessary to have a source of oxygen available at least occasionally to the alloy surface, to allow fresh oxide to form where the original protective layer may have been damaged, even just by slight movement. Without this supply of oxygen, no protective layer can form, and the exposed surface is at least, and probably more, reactive than that of a carbon steel. Pitting can certainly result, which can and has led to perforation of pipes in the past.
The other belief is that the more alloy additions made to the stainless steel the better. Again, this is not necessarily the case. 316L stainless steel is essentially an 18% chromium, 8% nickel and 2.5% molybdenum in iron alloy, with the advantage that the molybdenum imparts superior pitting resistance compared to the equivalent alloy without the molybdenum. This disadvantage is that it also promotes the presence of ferrite in the alloy and this ferrite is detrimental to the corrosion performance if exposed in hot concentrate nitric acid, i.e. 304L is better than 316L in this environment, to the extent that there used to be a ‘304NAG’ grade of particularly clean, low carbon and low impurity austenitic material, NAG standing for Nitric Acid Grade.
So, is stainless steel better than carbon steel? The answer is “On the one hand, yes. But on the other hand, no.”, as it is totally dependent on the environment and circumstance of the exposure as to which would be more cost effective and/or give the longer, or simply more predictable, service life.
So, which would I use? Sometimes one, sometimes the other, and being a typical materials engineer, sometimes neither!
Image: Jatinsanghvi [CC BY-SA 3.0 (https://creativecommons.org/licenses/by-sa/3.0)]