February 2019
Corrosion Resistant Alloys
Corrosion Resistant Alloys - Specialists in the right environment
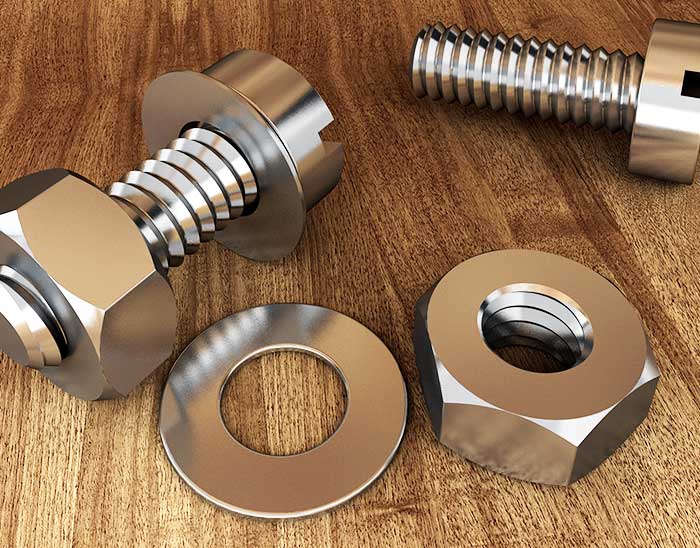
The family of metals known as Corrosion Resistant Alloys (CRAs) covers a wide variety of materials, but in the context of this article we'll be considering those alloys more corrosion resistant than the common stainless steels, so the higher alloyed austenitic stainless steels, nickel alloys, etc.
Firstly, CRAs are alloys whose corrosion resistance to certain environments is better than the commonly used stainless steels, e.g. the 304L or 316L grades. This family can include a range of higher alloy stainless steels, e.g. 310 (25% Cr, 20% Ni), 904L (25% Ni, 20% Cr), and the so called super austenitic stainless steels, 254SMo, 654SMO, 3RE65, Carpenter 20Cb3, etc., as well as the nickel alloys of the Incoloy, Inconel and Hastelloy families, Monels, some copper based alloys and even some aluminiums.
However, despite being such a diverse group, these alloys have one thing is common: the more specialised the intended application of the alloy (and some would say the higher the price), the less good it is in other environments.
Dr Hoyle explained: “A good example of this occurred to me a few years ago: A client asked why his Hasteloy C276 pump shaft kept corroding in 6 months when the original one lasted for years – what had changed with Hastelloy C276?
“The answer to the second part was simple – nothing. The answer to the first part was slightly more involved. The original shaft had indeed lasted for many years, as witnessed by the now rather tatty original drawing. The replacement shafts had been made to the original drawing dimensions and, it was claimed, material.
“Upon inspection of the drawing, the material was clearly identified and “Hastelloy”, followed by a rip which had removed any further designation. On reviewing the process chemistry, I asked the client how much a new shaft cost him. About £20k, including the effort to remove the old shaft, fit the new shaft, reinstall the pump and lost production.
“Okay, so was he prepared to take a £20k gamble on my say so? Given his rather desperate situation he said he would, so I suggested he have a new shaft made in Hastelloy Grade B2, rather than Hastelloy C276.
“Credit to him, he duly had it made and installed. Several years later it was still going strong.”
The moral of this is twofold: Firstly, referring to an alloy by a generic trade name and not a specific grade is a recipe for disaster; and secondly, if something worked well but no longer does, ask the question as to what has changed. It is often a lot simpler than is feared.
What this also illustrates is that in the right environment Hastelloy B2 can last years but Hastelloy C276 lasted only a matter of months. Why?
Simplistically, all CRAs rely on one of two corrosion protection mechanisms: either they are very reactive and form a protective compound on the surface (e.g. aluminium or chromium forming an oxide layer), or they are noble and don't readily react with the environment at all (e.g. gold, platinum, nickel, molybdenum). Hastelloy C276, with a 15% chromium content is one of the former types, relying on a thin oxide layer to form and protect the underlying metal, while Hastelly B2 is the second type, the 30% molybdenum in nickel being pretty noble and not reacting much at all.
This also means that Hastelloy C276 offers good protection in oxidising environments, where the protective layer can be repaired if damaged, whereas Hastelloy B2 does not rely on an oxide layer for protection and is good in reducing conditions. Sadly, Hastelloy B2 tends to corrode in oxidising conditions as the nobility of the alloy is insufficient to prevent some oxidation taking place.
And this phenomenon extends across many of the CRAs. Hastelloy G35 has been specifically developed for use in fluorine chemistry applications but is of limited use elsewhere. Inconel 718 has been developed for use in gas turbines / jet engines but isn't the best corrosion resistant alloy other than where these extremes of temperature and stress are involved. Lead has long been used in the sulphuric acid industry, even being suitable for use in batteries (lead acid batteries use a medium strength sulphuric acid, which readily attacks many other metals, but is effective as a long-term battery when used with pure lead). Lead has also demonstrated good service life in water systems, some Roman lead pipes still being serviceable after 2000 years, whereas steel may last a few years and even copper can be limited, particularly if the water contains minor organic acids (such as London bore hole waters). Copper alloys do find favour in seawater applications because of their corrosion resistance, high thermal conductivity (making them good in heat exchangers) and inherent resistance to biological fouling, ironically due to the dissolution of copper ions (corrosion) which does take place.
So where do the stainless steels fit in? Being iron based and containing at least 16% chromium (for austenitic grades) the common stainless steels are oxide protected, so suitable for oxidising or oxygen-containing environments. However, the big problem with the lower chromium alloyed versions are that chromium oxide is prone to attack by chlorides, ferric ions, cupric ions and even mercuric ions, meaning that pitting is prevalent in many situations. To some extent this can be reduced by adding more alloying additions, including molybdenum, more chromium, nickel (to control the metallurgical structure) and even copper, niobium and titanium. These alloys are never immune to pitting and corrosion, just more resistant.
At the extreme, gold and platinum are both noble metals which are reluctant to react with anything. That is not to say they cannot be corroded, it just takes a bit of effort to get them to!
So, the important thing about CRA’s is that what might be good in one environment is not necessarily any good in another. If in doubt, consult a competent Materials Engineer and seek advice but don't just assume that it'll be okay - that's a very expensive way of ensuring you'll have to do it all again.